Глаза боятся, руки делают…
Наконец я решил перейти от теории и экспериментов к практическим работам по доработке и электрификации модели ГАЗ-53А от Deagostini в масштабе 1/43.
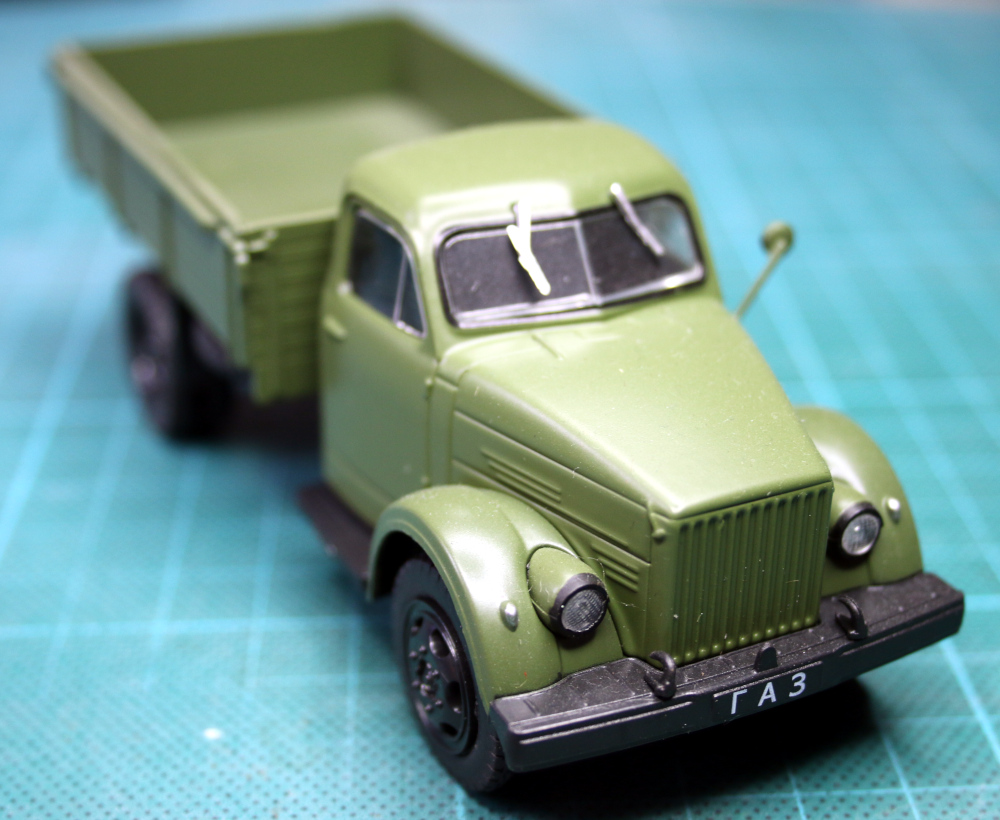
Внимательно ознакомившись с фото и видео материалами в группе VK «Электронные конверсии масштабных моделей», я принялся усердно думать — как бы мне сделать что-то подобное исходя из наличия материалов и инструментов? К счастью, ранее из Китая приехали конические шестерни (пары) от торговой марки Das87 — весьма качественные и ОЧЕНЬ дорогие!
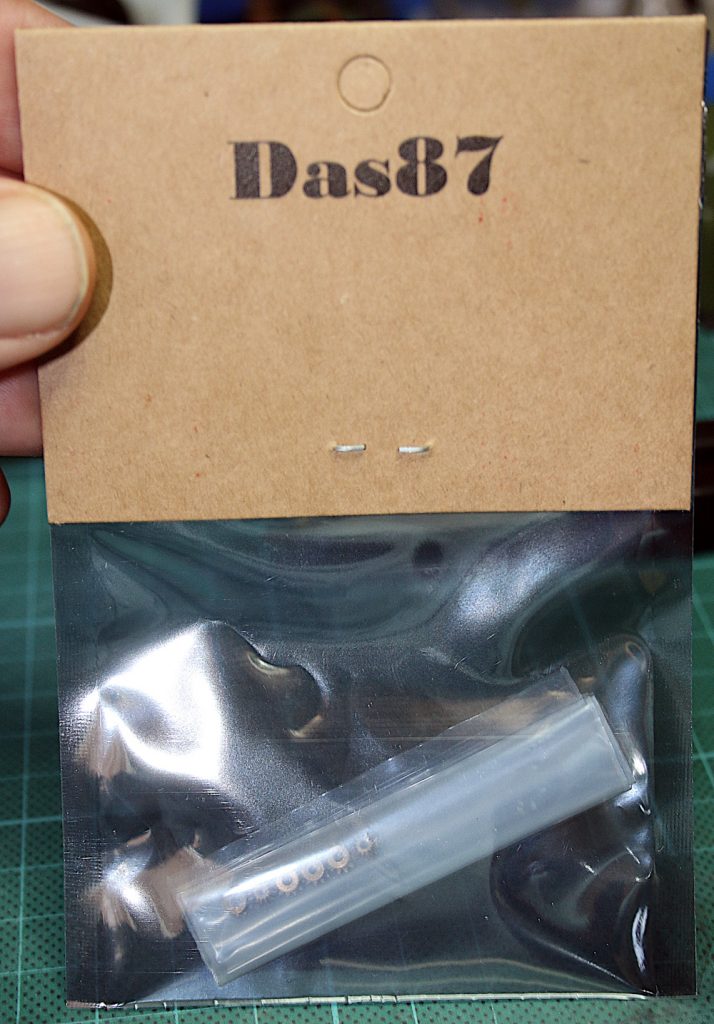
Вообще эти шестеренки предназначены для моделей масштаба 1/87, как видно из названия, но прочность латунного сплава из которого они сделаны позволяет передавать значительный крутящий момент и тянуть гораздо более крупные модели. Но прежде чем дать волю очумелым ручкам, мне пришлось уточнить размеры и набросать чертежик, чтобы было понятны остальные размеры для изготовления корпуса редуктора и всего моста.
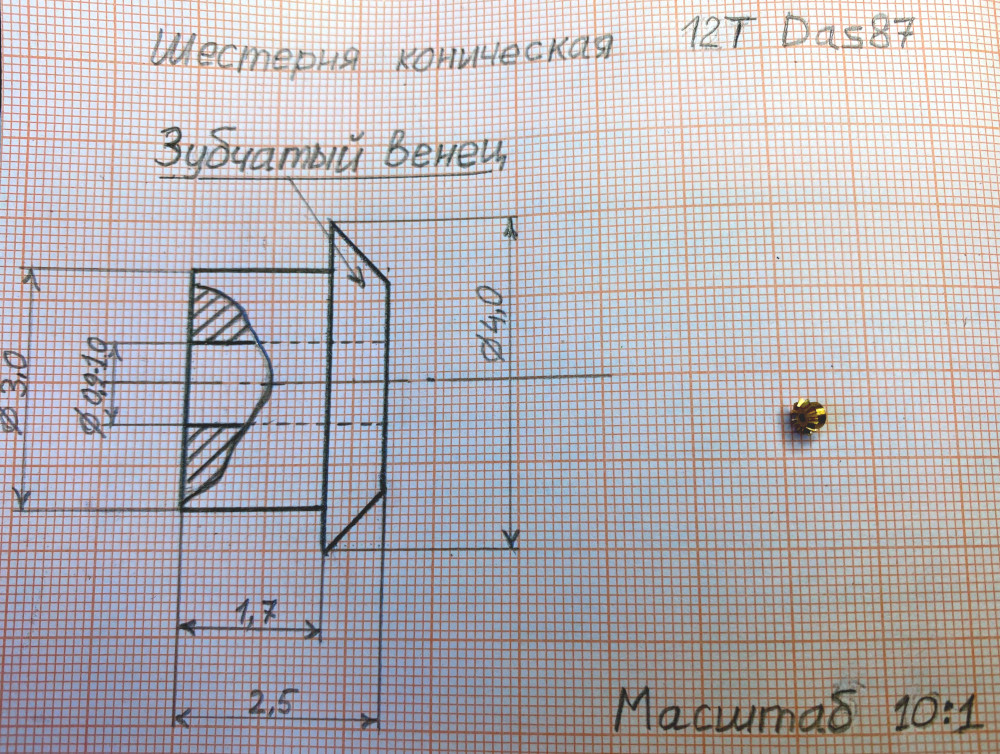
Теперь можно начать конструировать корпус редуктора. Начальным посылом к конструкции редуктора явилось наличие у меня тонкого медного листа толщиной 0,2 мм, причем медь уже отпущена, то есть хорошо гнется и не пружинит. Целью было получение развертки «коробочки» минимально возможных размеров, чтобы вписать готовый редуктор в штатную пластиковую деталь заднего моста модели ГАЗ-53А.
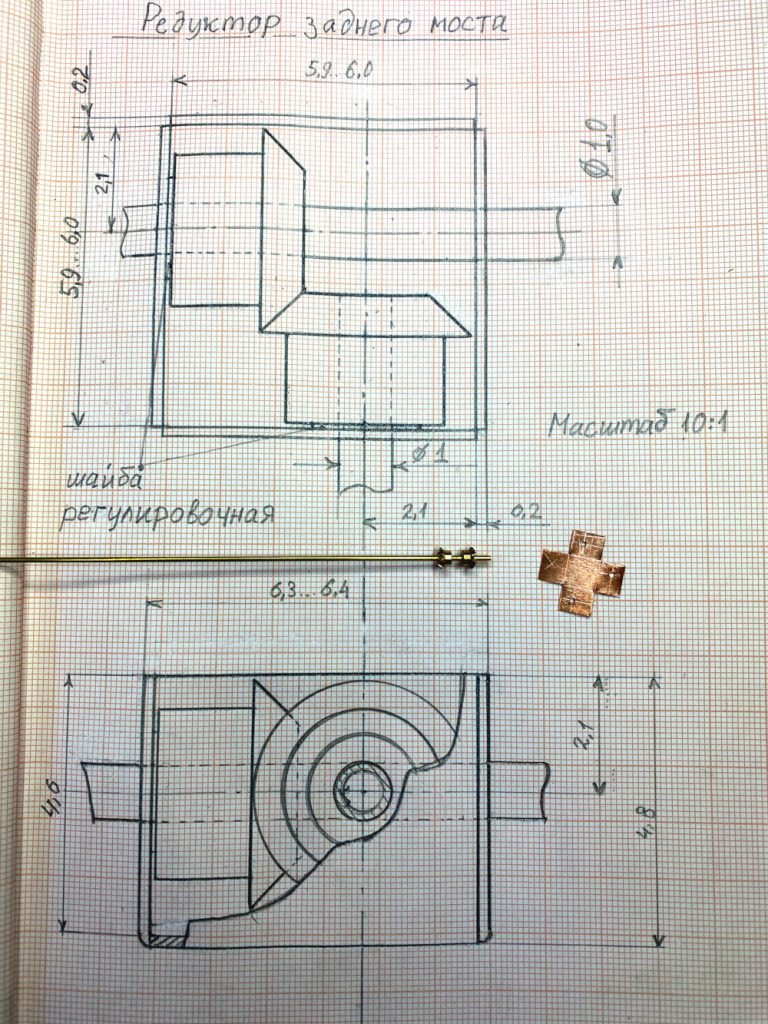
В качестве осей было решено использовать латунные трубочки диаметром 1 мм из запасов — год назад купил у наших восточных друзей набор трубок диаметром 0,1 мм — 1 мм с шагом 0,1 мм. Трубки достаточно прочные, но их легко резать и паять.
После вырезания развертки корпуса редуктора и сверления отверстий, тот ещё аттракцион без сверлильного станка, была согнута коробочка и собрано все с трубочками и шестеренками. В принципе, результат получился вполне приличный и работоспособный, но несколько хлипкий…
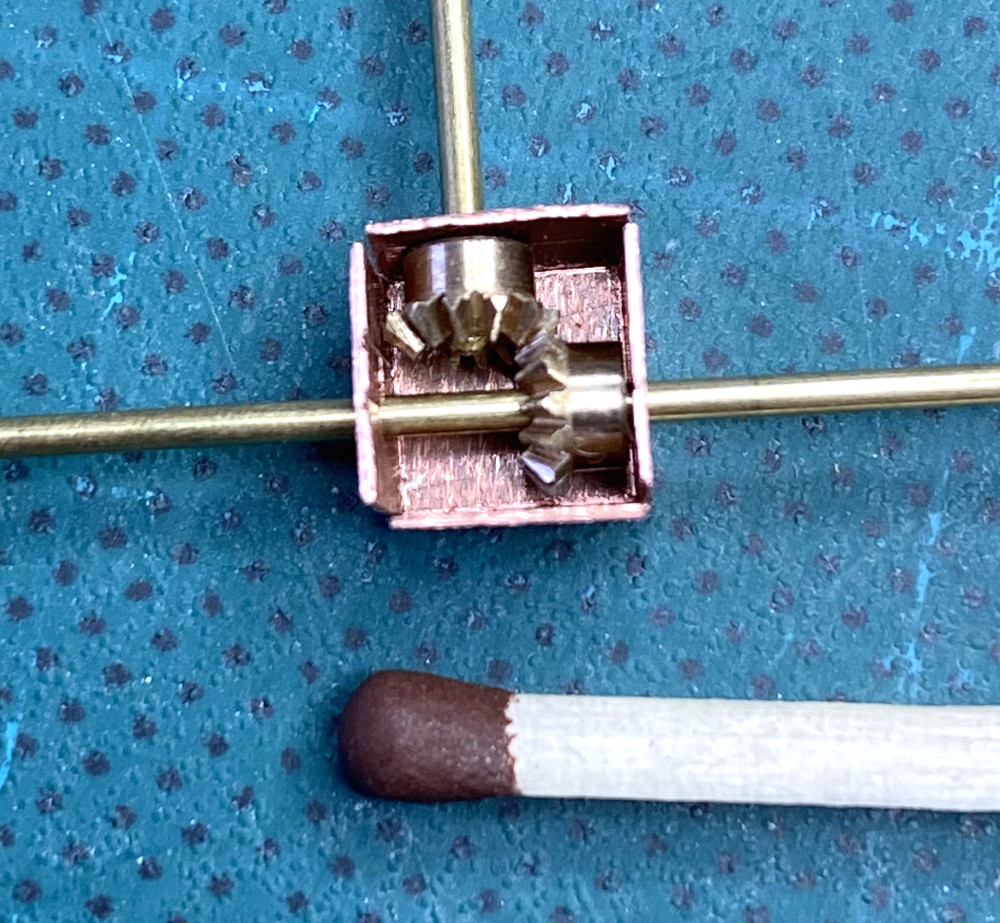
Конечно, чтобы придать окончательную прочность конструкции, можно запаять боковые рёбра корпуса, но тогда полностью теряется возможность регулировки зазоров между венцами шестеренок и устройство становится неразборным, а уверенности в получении чистого, без заеданий, вращения — не остается совсем.
Терзаем сомнениями, я все-таки решил сопоставить (примерить) получившийся редуктор с «родной» пластиковой деталью от модели…
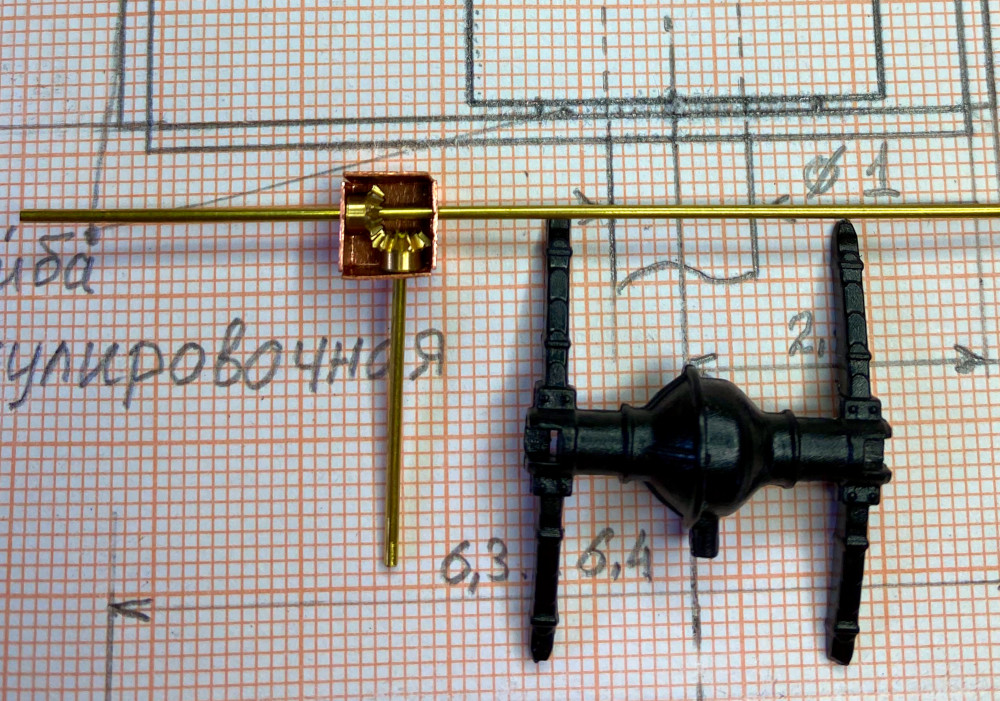
Теоретически, конечно «должен влезть», но очень уж впритык!
Кое-где стенки пластикового картера придется сточить в ноль, что пагубно скажется на общей прочности всей конструкции моста, а тогда всё это вообще теряет смысл — проще изготовить полностью весь мост из подручных материалов.
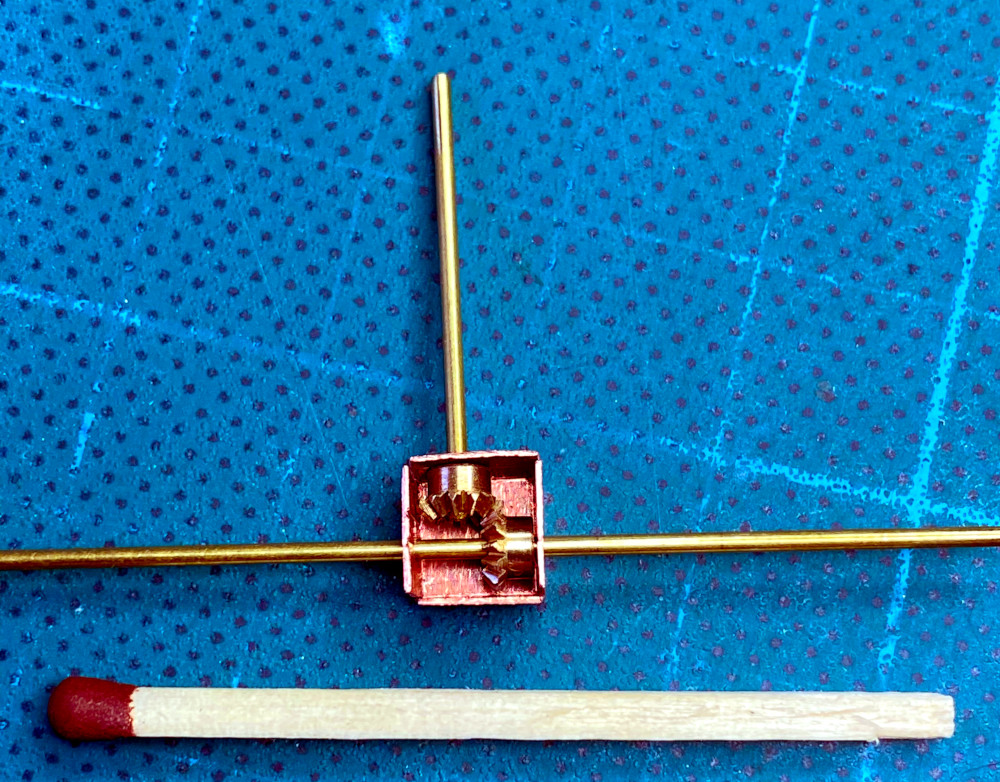
На сегодня — это всё! Пошел думать дальше…
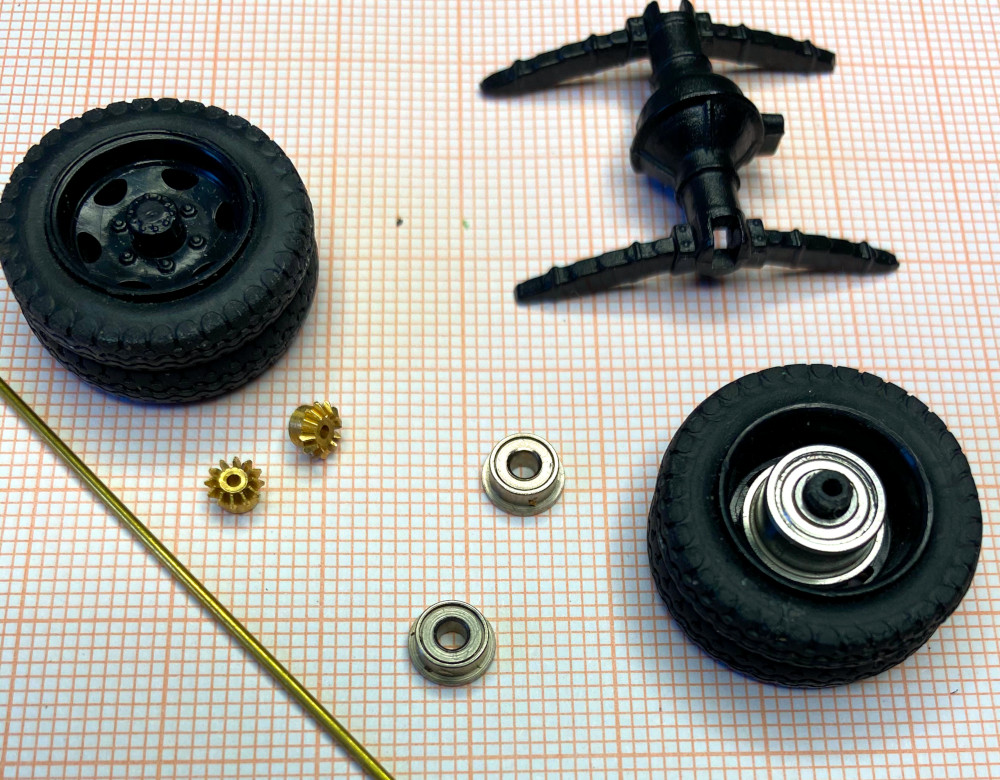
Всем добра!